Instrumentation
- INTENSO instrumentation solutions provide customized instrumentation systems from design to installation, and service. Our instrumentation team takes pride in their ability to meet project schedules and exceed expectations of our customers. In addition to the engineering and design support, calibration, commissioning, preventive maintenance, and start up assistance for any size and type of instrumentation project. Whatever your needs may be, INTENSO instrumentation team has the ability to get your project done on-time and on-budget.
- INTENSO instrumentation solutions typically consist of instrumentation hardware delivered through premier services such as consulting, specification, procurement, configuration, installation, commissioning, and start-up.
- The instrumentation team’s brand independence and objectivity allows them to deliver instrument packages properly applied to customer’s processes. INTENSO instrumentation team also provides services such as end user training, feasibility studies, and asset management systems.
INTENSO INSTRUMENTATION CAPABILITIES
- INTENSO has extensive relevant trade and management experience in instrumentation. Our personnel are skilled in both comprehensive electronic and select mechanical side disciplines. We take pride in our ability to meet demanding project schedules and exceed the expectations of our customers. Our experience and skills combine to provide our clients premier service with great depth in expertise. Our capabilities include new construction services, capital expansion, plant relocation, process consolidation, plant maintenance contracts, supplemental maintenance for routine or shutdown/turnaround activity.
- Instrument and control loop testing.
- Hydraulic and pneumatic tubing.
- Custom tubing layout and installation.
- Calibration and bench testing services.
- System evaluation and testing.
- Distributed control system (DCS).
- Programmable logic controllers (PLC).
- Microprocessor-based system control.
- Instrument panel and rack fabrication.
- Startup and checkout assistance.
- Shutdown and outage work.
- Maintenances planning.
- Return on investment feasibility studies.
- Efficiency studies.
PROJECT CONTROLS
- All INTENSO Projects are managed using proven techniques that have been extensively developed to ensure complete client fulfillment. These include:
• Instrument stands and supports.
• Flanged or threaded direct mount instruments.
• Environmental enclosures.
• Process tubing including pre-insulated, traced multi-tube bundles.
• Capillary type processing lines.
• Air drops (air supplies).
• Tube tray or raceway.
• Conduit for poly-tubing.
• Sample systems and panels.
TECHNICAL DISCIPLINES
- INTENSO can provide Certified Process Control Technicians for new construction or maintenance. Instrumentation Services we perform:
• Instrument Verification – This step involves checking all process controls against customer purchase orders to verify the instrument matches the purchase order and has not been damaged in shipment.
• Bench Calibration – This critical step involves verifying all set points, outputs, and ranges against the design criteria prior to installation. Each instrument receives a multi-point check to make sure it performs to owner specification. All control functions are checked, and if required, set points are programmed. Even “factory calibrated” instruments may be checked since shipping and handling can often disturb the settings. Bench calibration allows for a smoother progression in later phases of work such as loop check and start-up. There will be less chance of costly system upsets and delays caused by malfunctioning or non-calibrated hardware.
• Loop Check – This step involves signal checks after installation. Technicians go into the field and send actual signals from each transmitting device back to the controllers and from the controllers to the final control element. This can be accomplished using simulated signals (dry) or by filling the system with inert fluids or gases to simulate the actual process conditions (wet). Loop checks let the owner know everything has been installed properly, is functioning and ready for start-up.
• Start-up & Commissioning – The final step in the process is start-up. Having verified all loops and control functions the technician can now “start-up” each system. This is accomplished with engineering support from the owner or owner’s representatives. Specialty vendors may also be called in to support any non-conventional hardware.
• Each step of this process is documented per owner requirements. All calibration test standards may be certified by an independent calibration laboratory and are fully traceable.
PREVENTATIVE MAINTENANCE SERVICES
- INTENSO has expertise in the maintenance of process control related equipment using a wide variety of applications (analog, digital, pneumatic, hydraulic, programmable logic control, distributed control systems). Our client’s instrumentation is monitored by a tracking software that will indicate due dates and trends in calibration errors. INTENSO can support most every Quality System. INTENSO adheres to ISA and ANSI standards. INTENSO calibration data reporting system provides all necessary documentation.
QUALITY ASSURANCE
- Our Quality Assurance Program describes the control procedures implemented by INTENSO ensuring the quality of instrumentation control installation or maintenance.
Our QA Program Documents
- Certify all Test Equipment to ISA standards.
Document and traceability all Activities
- Control Documents, Inspect and Pressure Test Installations, Ensure Correct Installations.
Additional Services Provided
- Supplementing of In-House Maintenance Staff, Off Site Warehousing
OUR SERVICES
WHY CHOOSE US
- We have wide range of electrical experience.
- We have honest, hardworking and committed team.
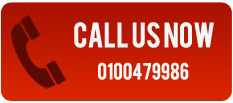